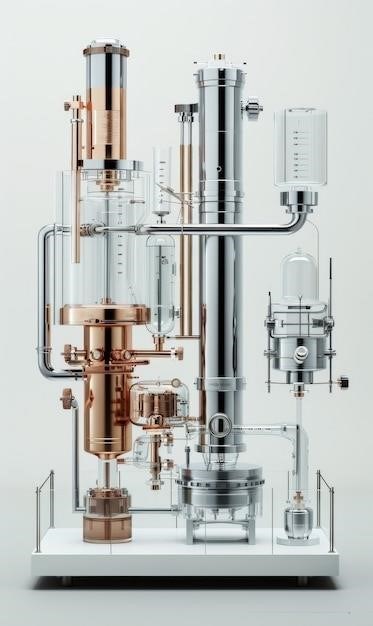
Valve Manual⁚ A Comprehensive Guide
This manual provides a comprehensive overview of manual valves, covering their types, mechanisms, applications, advantages, disadvantages, maintenance, troubleshooting, and safety considerations․ It is intended for individuals involved in the design, selection, installation, operation, and maintenance of manual valves in various industrial settings․
Introduction
Manual valves are fundamental components in fluid handling systems, playing a crucial role in controlling the flow of liquids and gases․ These valves are operated manually, typically by a handwheel, lever, or other mechanical means, allowing for direct control over the flow path․ Manual valves are widely employed in various industries, including manufacturing, power generation, water treatment, and chemical processing, due to their simplicity, reliability, and cost-effectiveness․ This manual aims to provide a comprehensive understanding of manual valves, encompassing their different types, mechanisms, applications, advantages, disadvantages, maintenance procedures, troubleshooting techniques, and safety considerations․
Types of Manual Valves
Manual valves come in a wide variety of designs, each suited for specific applications and flow conditions․ Some of the most common types include⁚
- Ball Valves⁚ Featuring a spherical ball with a bore through its center, ball valves provide a simple and efficient way to control flow․ They are typically used for on/off applications due to their quick opening and closing action․
- Gate Valves⁚ These valves consist of a gate that moves perpendicular to the flow direction, either opening or closing the flow path․ They are generally used for large-scale flow control and are suitable for both throttling and on/off operations․
- Globe Valves⁚ Globe valves utilize a disc-shaped plug that moves perpendicular to the flow direction, creating a throttling effect․ They are often used for flow regulation and control in high-pressure applications;
- Butterfly Valves⁚ Butterfly valves feature a disc-shaped plate that rotates within the flow path, controlling the flow by varying the opening․ They are commonly used in applications requiring quick and easy flow control․
- Diaphragm Valves⁚ These valves employ a flexible diaphragm to regulate flow․ The diaphragm is typically made of rubber or other resilient material and provides a tight seal, making them ideal for applications handling corrosive or abrasive fluids․
The selection of the appropriate valve type depends on factors such as the fluid being handled, pressure, temperature, flow rate, and specific operational requirements․
Ball Valves
Ball valves are a common and versatile type of manual valve, characterized by their simple design and efficient operation․ They consist of a spherical ball with a bore through its center, which rotates within a housing to control the flow of fluid․ The ball has a port that aligns with the flow path when the valve is open, allowing fluid to pass through․ When the ball is rotated, the port is blocked, effectively shutting off the flow․
Ball valves are typically used for on/off applications due to their quick opening and closing action, making them suitable for situations where rapid flow control is essential․ They are also known for their low pressure drop, minimal maintenance requirements, and durability․ Ball valves are commonly found in various industries, including water treatment, chemical processing, oil and gas, and general industrial applications․
Gate Valves
Gate valves are designed for on/off applications and are typically used in situations where a tight seal is required for prolonged periods․ Their primary function is to completely obstruct or allow the flow of fluid through a pipeline․ They consist of a gate, typically a wedge-shaped disc, that slides vertically across a seat within the valve body․ When the gate is raised, it allows fluid to flow through, and when it is lowered, it blocks the flow․
Gate valves are best suited for applications with minimal pressure drops, as they offer low resistance to flow when fully open․ However, their gradual opening and closing action make them less ideal for quick flow control․ They are commonly employed in pipelines, water distribution systems, and other applications where reliable isolation is critical․
Globe Valves
Globe valves are known for their ability to regulate flow, making them suitable for throttling applications․ They feature a disc-shaped plug that moves vertically within a seat, controlling the flow path․ The plug’s movement is controlled by a stem connected to a handwheel․ As the plug is raised, the flow path opens, allowing fluid to pass through․ Conversely, lowering the plug restricts the flow, allowing for precise control․
Globe valves are often used in applications requiring precise flow regulation, such as pressure control systems, heating and cooling systems, and chemical processes․ While they offer excellent control over flow rates, they also tend to create a greater pressure drop across the valve compared to other types, which can lead to energy losses․
Butterfly Valves
Butterfly valves are characterized by their simple design and ease of operation․ They consist of a disc-shaped plate, or “butterfly,” mounted on a shaft that rotates within a circular housing․ The butterfly is typically positioned perpendicular to the flow direction when closed, blocking the flow path․ Rotating the shaft 90 degrees aligns the butterfly with the flow, allowing fluid to pass through․
Butterfly valves are commonly used in applications where a quick-opening and closing action is required, such as in large-diameter pipelines, ventilation systems, and water distribution networks․ They offer low pressure drop and are relatively inexpensive compared to other valve types․ However, they may not be suitable for high-pressure applications or those requiring precise flow control due to their inherent design limitations․
Diaphragm Valves
Diaphragm valves are known for their ability to handle abrasive, corrosive, or viscous fluids, making them suitable for a variety of industrial applications․ These valves employ a flexible diaphragm, often made of rubber or synthetic materials, that acts as a barrier between the fluid and the valve mechanism․ The diaphragm is typically held in place by a plate or a ring, which can be lifted or lowered to open or close the valve․
When the diaphragm is raised, fluid can flow through the valve․ Lowering the diaphragm seals the flow path, preventing the passage of fluid․ Diaphragm valves offer several advantages, including their ability to handle slurries, solids, and highly corrosive substances․ They are also known for their leak-tight sealing capabilities and their resistance to wear and tear․ However, diaphragm valves may have limited temperature and pressure ratings, and their maintenance can be more involved than other types of valves․
Mechanism and Function
Manual valves rely on a simple yet effective mechanism to control fluid flow․ They typically consist of a valve body, a sealing element (such as a ball, gate, or diaphragm), and a manual operator․ The operator, which can be a handwheel, lever, or gear, is connected to the sealing element․ By turning or moving the operator, the sealing element is positioned to either block or allow fluid flow through the valve․
The function of a manual valve is to regulate fluid flow by starting, stopping, or throttling the flow rate․ They can be used to isolate sections of a pipeline, control the pressure within a system, or direct the flow of fluid in a specific direction․ Manual valves are often employed in situations where automation is not required, such as in low-pressure systems, for cost-effective solutions, or when manual intervention is desired for safety or operational reasons․
Applications of Manual Valves
Manual valves find wide applications across various industries due to their simplicity, reliability, and cost-effectiveness․ They are commonly used in⁚
- Industrial Plants⁚ Manual valves are essential for controlling fluid flow in processes like steam systems, chemical processing, and manufacturing․ They are used for isolation, throttling, and directing fluid in various stages of production․
- Construction Machinery⁚ Manual valves are employed in hydraulic systems of construction equipment like excavators, cranes, and bulldozers․ They regulate the flow of hydraulic fluid to control the movement of actuators and cylinders․
- Agriculture⁚ Manual valves are used in irrigation systems, water distribution networks, and agricultural machinery․ They control the flow of water for irrigation, drainage, and other agricultural operations․
- Automotive Engineering⁚ Manual valves are used in hydraulic systems of vehicles, particularly in braking systems, steering systems, and suspension systems․ They control the flow of hydraulic fluid to activate brakes, steer the vehicle, and adjust suspension components․
Manual valves are also used in domestic applications, such as water supply systems, gas lines, and plumbing systems․ They are often found in valves for sinks, showers, and toilets․
Advantages and Disadvantages
Manual valves offer a number of advantages, making them a popular choice in many applications⁚
- Simplicity and Reliability⁚ Manual valves are relatively simple in design and construction, leading to high reliability and ease of maintenance․ They are less prone to failure compared to more complex automated valves․
- Cost-Effectiveness⁚ Manual valves are generally more affordable than automated valves, making them an attractive option for budget-conscious projects․
- Direct Control⁚ Manual valves provide direct control over fluid flow, allowing for precise adjustments and immediate responses to changing conditions․
- Safety in Emergency Situations⁚ In case of power outages or system failures, manual valves provide a backup mechanism for controlling fluid flow, ensuring safety and preventing accidents․
However, manual valves also have some disadvantages⁚
- Manual Operation⁚ Manual valves require human intervention for operation, which can be inconvenient, time-consuming, and prone to human error․
- Limited Applications⁚ Manual valves are not suitable for applications requiring frequent or rapid adjustments in fluid flow or for highly automated processes․
- Potential for Wear and Tear⁚ Manual operation can lead to wear and tear on valve components, requiring regular maintenance and replacement․
The decision to use manual valves depends on the specific application, its requirements, and the available resources․
Maintenance and Troubleshooting
Regular maintenance is crucial for ensuring the longevity and proper functioning of manual valves․ A well-maintained valve operates smoothly and reliably, preventing leaks, malfunctions, and safety hazards․
- Visual Inspection⁚ Conduct regular visual inspections for signs of wear, damage, corrosion, or leaks․ Check for loose bolts, cracked seals, or damaged valve stems․
- Lubrication⁚ Lubricate moving parts, such as valve stems and handwheels, with an appropriate lubricant․ This reduces friction, improves operation, and extends valve life․
- Cleaning⁚ Clean the valve body, stem, and surrounding area to remove debris, dirt, or other contaminants that can hinder proper operation․
- Packing Replacement⁚ Replace packing as needed to maintain a tight seal and prevent leaks․ This is essential for valves handling hazardous fluids․
- Testing⁚ Test the valve regularly to ensure it opens and closes fully and smoothly․ Check for leaks in the closed position․
When troubleshooting a manual valve, begin by identifying the problem․ Common issues include leaks, sticking, and incomplete opening or closing․ Consult the valve manufacturer’s instructions for detailed troubleshooting procedures and repair recommendations․
Safety Considerations
Manual valves play a vital role in controlling fluid flow, but their operation also presents potential safety hazards․ It’s crucial to prioritize safety during all stages of valve handling, from installation to operation and maintenance․
- Pressure Relief⁚ Ensure adequate pressure relief devices are installed upstream of manual valves to prevent over-pressurization and potential catastrophic failure․
- Lockout/Tagout: Implement lockout/tagout procedures before working on any valve․ This ensures the valve is isolated from the system and prevents accidental activation during maintenance or repairs․
- Personal Protective Equipment (PPE)⁚ Use appropriate PPE, including gloves, safety glasses, and footwear, when handling valves․ This protects against potential hazards like leaks, spills, or high-pressure releases․
- Proper Training⁚ Provide thorough training to operators and maintenance personnel on safe valve operation, maintenance procedures, and emergency response protocols․
- Emergency Procedures⁚ Develop and implement clear emergency procedures for handling valve malfunctions, leaks, or other incidents․ This ensures a swift and coordinated response to minimize risks and potential injuries․
By adhering to these safety considerations, you can mitigate risks and create a safer working environment for all personnel involved in the operation and maintenance of manual valves․