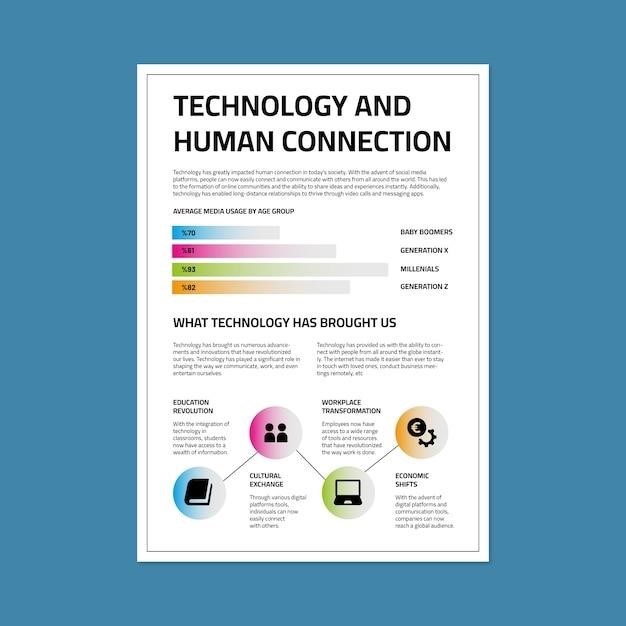
AS5202 Specification⁚ A Comprehensive Overview
This document provides specifications for aerospace standard port or fitting ends with internal straight threads according to design standard AS5202. It provides information on where to purchase the standard and submit proposed changes, and notes that MS33649 (AS5202) ― solid pilot port is a common application of this standard.
Introduction to AS5202
AS5202, formally known as SAE AS5202, is a widely recognized standard in the aerospace industry that defines the specifications for port or fitting ends featuring internal straight threads. This standard serves as a crucial guide for ensuring compatibility, reliability, and safety in various aerospace applications. The AS5202 standard ensures that components designed to work together will have consistent and reliable connections, minimizing the risk of leaks, malfunctions, or failures during critical operations. This document provides comprehensive guidance on the design, construction, and materials used in accordance with AS5202, ensuring adherence to rigorous quality and performance standards.
Key Features and Applications of AS5202
AS5202 is renowned for its key features that contribute to its widespread adoption in aerospace applications. These features include⁚
- Precision Design⁚ AS5202 specifies precise dimensions for the port or fitting ends, ensuring consistent and reliable connections between components. This precision is crucial for maintaining the integrity of fluid systems and preventing leaks.
- Internal Straight Threads⁚ The standard mandates the use of internal straight threads, which provide robust and secure connections that can withstand high pressures and vibrations commonly encountered in aerospace environments.
- Material Specifications⁚ AS5202 outlines specific material requirements for the construction of port and fitting ends, ensuring that they meet the demanding performance and durability standards of the aerospace industry.
The AS5202 standard finds application in a wide range of aerospace systems, including⁚
- Aircraft Fuel Systems⁚ AS5202 is essential for ensuring the safe and reliable operation of aircraft fuel systems, where leaks or malfunctions could have catastrophic consequences.
- Hydraulic Systems⁚ AS5202 is used in hydraulic systems that power various functions on aircraft, such as landing gear, flaps, and brakes.
- Pneumatic Systems⁚ AS5202 is also utilized in pneumatic systems that control various aspects of aircraft operation, such as air conditioning and pressurization.
Understanding the AS5202 Standard
AS5202, formally known as SAE AS5202, is a crucial standard in the aerospace industry, defining the specifications for aerospace standard port or fitting ends with internal straight threads. The standard’s comprehensive nature encompasses various aspects, including⁚
- Dimensional Requirements⁚ AS5202 specifies precise dimensions for various parameters, such as thread diameter, thread length, and overall length of the port or fitting end. These dimensions are critical for ensuring compatibility and proper sealing between components.
- Material Specifications⁚ The standard outlines specific material requirements for the construction of port and fitting ends, ensuring that they meet the demanding performance and durability standards of the aerospace industry. These materials are typically high-strength alloys capable of withstanding extreme temperatures, pressures, and vibrations.
- Performance Criteria⁚ AS5202 also outlines performance criteria, including pressure ratings, temperature limits, and resistance to corrosion. These criteria ensure that the port and fitting ends can withstand the harsh conditions encountered in aerospace applications.
Historical Context
The AS5202 standard has its roots in the military aerospace industry, initially emerging as a specification under the designation MS33649. This specification, developed by the United States Department of Defense, aimed to standardize the design and construction of port and fitting ends used in military aircraft and related systems. Over time, the standard gained broader acceptance within the aerospace industry, leading to its adoption by SAE (Society of Automotive Engineers) as AS5202. The transition from a military-specific standard to a broader industry standard reflects the critical role of AS5202 in ensuring interoperability and consistent quality in aerospace applications. The standard’s historical context underscores its importance in the development and evolution of aerospace technology.
Design and Construction
AS5202 defines a specific design and construction for aerospace port and fitting ends with internal straight threads. The standard outlines key dimensions and tolerances for these components, ensuring compatibility and interchangeability between different manufacturers. The design emphasizes robust construction to withstand the demanding conditions of aerospace applications. The standard specifies the use of materials and manufacturing processes that meet stringent quality standards, including detailed specifications for heat treatments and surface finishes. These design and construction requirements are crucial for maintaining the integrity and reliability of aerospace systems, where failure is not an option;
Material Specifications
AS5202 specifies the materials used in the construction of aerospace port and fitting ends with internal straight threads. These materials must meet stringent requirements for strength, corrosion resistance, and compatibility with other aerospace components. Common materials include high-strength alloys like stainless steel, titanium, and aluminum. The standard details the specific grades and types of materials allowed for different sizes and applications. It also provides guidance on heat treatments and surface finishes to ensure the desired mechanical properties and corrosion resistance. These material specifications are critical for maintaining the integrity and reliability of aerospace systems, where failure is not an option.
AS5202 in Aerospace Applications
AS5202 plays a vital role in various aerospace applications, defining the standard for port and fitting ends with internal straight threads used in aircraft systems. These components are crucial for connecting and sealing fluid lines, fuel systems, hydraulic systems, and other critical components. AS5202 ensures that these connections are reliable and withstand the harsh environments encountered in aviation. The standard covers a wide range of sizes and configurations to accommodate different system requirements. Its use ensures compatibility and interchangeability between components from different manufacturers, simplifying maintenance and repair operations within the aerospace industry.
Port and Fitting End Types
AS5202 outlines several port and fitting end types, each designed for specific applications and requirements within aerospace systems. The standard defines these components based on their size, thread configuration, and sealing mechanisms. Common types include straight thread ports, which offer a simple and reliable connection for various fluid lines. Additionally, the standard includes specifications for threaded fittings, such as hex-head fittings and flanged fittings, which are used to connect and seal components in different configurations. The standard also provides guidance on the selection of appropriate O-ring sizes and materials for sealing these connections, ensuring leak-proof performance in demanding aerospace environments.
Applications in Aircraft Systems
AS5202 plays a critical role in the design and construction of various aircraft systems, ensuring reliable connections and sealing for critical components. The standard is used in a wide range of applications, including fuel systems, hydraulic systems, pneumatic systems, and environmental control systems. AS5202 ports and fittings are integral to connecting fuel tanks, pumps, filters, and other critical components in fuel systems. In hydraulic systems, they ensure secure connections for hydraulic actuators, valves, and other components that control flight surfaces and landing gear. AS5202 ports and fittings are also essential for connecting air conditioning units, oxygen systems, and other components in aircraft environmental control systems. The standard’s focus on high-quality materials, precision machining, and rigorous testing ensures that these connections can withstand the extreme pressures, temperatures, and vibrations encountered in aircraft operation.
Integration with Other Aerospace Standards
AS5202 seamlessly integrates with other prominent aerospace standards, fostering interoperability and ensuring consistency in design and construction. It complements standards such as SAE AS5864 and SAE AS5863, which define specific requirements for aerospace fluid connectors and hose assemblies. This integration allows for a cohesive and standardized approach to fluid handling systems in aircraft, simplifying the design and maintenance processes. The compatibility with these standards guarantees that AS5202 ports and fittings can be readily incorporated into existing systems, facilitating the use of standardized components throughout the aircraft. The standard’s adherence to these industry-recognized standards ensures that AS5202 ports and fittings meet the stringent requirements for safety, reliability, and performance in the demanding aerospace environment.
AS5202 vs. Other Standards
AS5202, while widely used in aerospace applications, stands alongside other industry standards that cater to specific requirements. A comparison with these standards reveals the unique characteristics and strengths of AS5202. MS33649, a closely related standard, shares similarities with AS5202 in defining aerospace port or fitting ends with internal straight threads. However, AS5202 often serves as a more comprehensive and updated standard, incorporating advancements in design and manufacturing practices. SAE J1926, another relevant standard, focuses on fluid connectors and hose assemblies, offering specifications that complement AS5202. AS5202 often complements SAE J1926 by providing detailed specifications for the port or fitting end itself. ISO 3161, a globally recognized standard, outlines requirements for hydraulic fittings, offering a broader scope than AS5202. While AS5202 specifically addresses aerospace applications, ISO 3161 provides specifications for various industries, including aerospace. Understanding the nuances and differences between these standards allows engineers and manufacturers to select the most appropriate standard for their specific needs, ensuring compatibility and adherence to industry best practices.
Comparison with MS33649
AS5202 and MS33649 are closely related standards, both focusing on aerospace port or fitting ends with internal straight threads. While they share fundamental similarities, there are distinctions that set them apart. AS5202 is often considered a more comprehensive and updated standard, incorporating advancements in design and manufacturing practices. MS33649, while still widely used, may lack the latest updates and refinements found in AS5202. Furthermore, AS5202 may cover a broader range of port and fitting end types, providing a more diverse set of specifications. However, MS33649 remains a valuable standard for certain applications, particularly those requiring compatibility with legacy systems or specific design requirements. Ultimately, the choice between AS5202 and MS33649 depends on the specific needs of the application, taking into account factors such as design requirements, compatibility, and availability of resources;
Comparison with SAE J1926
SAE J1926 and AS5202 are both important standards in the aerospace industry, but they serve different purposes. While AS5202 focuses on the specifications for port and fitting ends with internal straight threads, SAE J1926 governs the design of bosses and associated components. In essence, AS5202 defines the interface between the fitting and the system, while SAE J1926 addresses the design of the system itself. This means that AS5202 and SAE J1926 are often used together to ensure compatibility and proper integration of components. For instance, the dimensions of the AS5202 port must be compatible with the boss defined by SAE J1926 to ensure a secure and leak-proof connection. Both standards contribute to the overall safety and reliability of aerospace systems, ensuring that components function as intended and meet the stringent requirements of the aviation industry.
Comparison with ISO 3161
While both AS5202 and ISO 3161 are standards that define specifications for aerospace connectors, they differ in their scope and focus. AS5202 primarily addresses internal straight thread port and fitting ends, while ISO 3161 encompasses a broader range of connectors, including those with external threads, as well as other types like quick-disconnect couplings and bayonet-style connectors. This difference in scope reflects the distinct design philosophies and application requirements of the organizations behind these standards. AS5202 is primarily used within the US aerospace industry, while ISO 3161, being an international standard, enjoys wider adoption across the globe. Despite these differences, both standards play a crucial role in ensuring the interoperability and reliability of aerospace systems, fostering a global framework for consistent connector design and manufacturing.
Resources and Documentation
For those seeking to delve deeper into the nuances of AS5202, numerous resources are available to provide comprehensive information and support. The official AS5202 PDF specifications, readily accessible online, offer a definitive guide to the standard’s requirements and guidelines. These documents are typically hosted by reputable organizations like the SAE International (Society of Automotive Engineers) and the Aerospace Industries Association (AIA), serving as a valuable reference for engineers, manufacturers, and other stakeholders. Additionally, numerous online databases and repositories provide access to AS5202-related documentation, technical articles, and case studies, enriching the understanding and application of the standard. For those seeking practical guidance and support, industry suppliers and manufacturers specializing in aerospace connectors are a valuable resource, offering technical expertise, product catalogs, and tailored solutions based on the AS5202 standard.
AS5202 PDF Specifications
The core of AS5202 documentation lies in its official PDF specifications. These documents, often available for purchase or download from organizations like SAE International, provide a comprehensive guide to the standard’s requirements and guidelines. They detail critical aspects such as dimensional tolerances, material specifications, design considerations, and testing procedures, ensuring consistency and reliability in aerospace connector design and manufacturing. The PDF specifications are essential for engineers, manufacturers, and quality assurance personnel involved in the development and implementation of AS5202-compliant connectors. They serve as a definitive reference for ensuring adherence to the standard’s stringent requirements and contributing to the overall safety and performance of aerospace systems.
Online Resources and Databases
The digital age has transformed access to technical information, making AS5202 specifications readily available online. Numerous resources and databases cater to the needs of engineers, manufacturers, and researchers seeking detailed insights into this standard. SAE International’s website, for example, offers a dedicated section for aerospace standards, including AS5202, often with downloadable PDFs or access to online versions. Other reputable organizations, such as the Aerospace Industries Association (AIA), provide links to relevant documents and resources. These online platforms streamline access to the latest revisions, updates, and interpretations of AS5202, ensuring that users have the most current and accurate information at their fingertips. Additionally, specialized databases like the Aerospace Standards Database (ASD) offer comprehensive search functionality, allowing users to quickly locate specific sections or requirements within the AS5202 specifications, further simplifying research and analysis.
Industry Suppliers and Manufacturers
The practical application of AS5202 hinges on the expertise of industry suppliers and manufacturers who specialize in producing components that adhere to this standard. These companies play a vital role in the aerospace industry, providing high-quality parts that meet the rigorous demands of aircraft and spacecraft. Suppliers of AS5202-compliant components often possess extensive knowledge of the standard’s intricacies, ensuring that their products meet the precise specifications and tolerances outlined. They offer a wide range of components, including ports, fittings, and other related parts, designed to seamlessly integrate into aerospace systems. Manufacturers specializing in AS5202-compliant components often invest in advanced manufacturing technologies and quality control processes to ensure product consistency and reliability. Their commitment to adhering to the AS5202 standard is paramount, as it guarantees the safety and performance of the aerospace systems they contribute to.
The AS5202 specification stands as a cornerstone for ensuring the integrity and functionality of aerospace systems by standardizing the design and construction of port and fitting ends with internal straight threads. Its comprehensive nature, encompassing historical context, design principles, material specifications, and compatibility with other aerospace standards, makes it an indispensable tool for engineers, manufacturers, and other stakeholders involved in aerospace development and maintenance. By adhering to the AS5202 standard, the aerospace industry fosters a high level of interoperability, reliability, and safety, contributing to the success of crucial aeronautical and space endeavors. The continued evolution and application of AS5202 will undoubtedly play a significant role in the future of aerospace technology, ensuring that the industry continues to innovate while maintaining the highest standards of performance and safety.