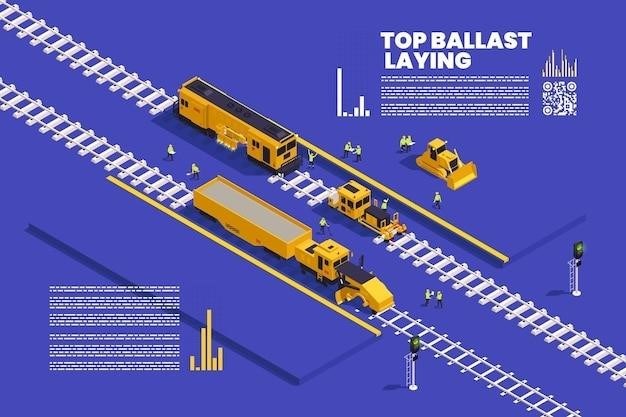
Linear Guide Rails⁚ An Overview
Linear guide rails, also known as slide rails, linear rails, or linear sliders, are mechanical components that support and guide moving parts in a straight line. They are crucial for precise linear motion in industrial applications, such as machine tools, automation systems, and robotics. Linear guide rails are designed to provide smooth, low-friction movement while handling significant loads, making them essential for various industries.
What are Linear Guide Rails?
Linear guide rails are essential components in linear motion systems, providing a precise and controlled path for moving parts. These rails are typically made of hardened steel and feature a precisely machined surface that allows for smooth and accurate linear movement. They are often found in industrial applications, such as machine tools, automation systems, and robotics, where smooth and precise linear motion is crucial for optimal performance.
A linear guide rail system consists of two main components⁚ a rail and a carriage. The rail serves as a fixed guide, providing a straight path for the carriage to move along. The carriage, which is attached to the moving part, houses linear bearings that roll along the rail, reducing friction and providing smooth, accurate movement.
Types of Linear Guide Rails
Linear guide rails are categorized based on the type of bearing used, which determines their load capacity, speed, and precision. The most common types include⁚
- Ball Bearing Linear Guide Rails⁚ These rails utilize recirculating balls for low friction and high speed operation. They are suitable for applications requiring high precision and smooth linear motion.
- Roller Bearing Linear Guide Rails⁚ Featuring rolling elements with a larger contact area, these rails offer higher load capacity and rigidity compared to ball bearing rails. They are ideal for applications with heavy loads and demanding operating conditions.
- Linear Slides⁚ These rails are often used for lighter loads and provide a simple and cost-effective solution for linear motion. They are commonly found in consumer products and less demanding industrial applications.
The choice of linear guide rail type depends on factors such as load capacity, speed, precision requirements, and environmental conditions.
Applications of Linear Guide Rails
Linear guide rails are ubiquitous in various industries, enabling precise linear motion in countless applications. Some notable examples include⁚
- Machine Tools⁚ Linear guide rails are essential components in machine tools, such as CNC machining centers, lathes, and milling machines. They ensure accurate positioning of cutting tools and workpieces, leading to high precision and surface finish.
- Automation Systems⁚ In automated production lines, linear guide rails are crucial for moving parts, assemblies, and products along defined paths. They enable efficient and precise material handling, assembly operations, and packaging processes.
- Robotics⁚ Linear guide rails are often used in robotic arms and manipulators for precise movement and positioning. They allow robots to perform tasks such as welding, painting, and assembly with accuracy and repeatability.
- Medical Equipment⁚ Linear guide rails find applications in medical equipment, such as surgical robots, X-ray machines, and imaging systems. They provide smooth and controlled movement for precise positioning and operation.
- Printing and Packaging⁚ In printing and packaging industries, linear guide rails ensure accurate and repeatable movement of printing heads, cutting blades, and other components. They contribute to consistent quality and high-speed production.
These are just a few examples of the diverse applications of linear guide rails, demonstrating their importance in modern manufacturing and technology.
Components of a Linear Guide Rail System
Linear guide rail systems consist of three primary components⁚ the rail, the carriage, and linear bearings.
The Rail
The rail is the foundational element of a linear guide rail system, serving as the stationary track for the moving carriage. It is typically made of hardened steel, ensuring high rigidity and durability. The rail’s profile is precisely machined to provide a smooth, accurate surface for the carriage to travel on. The rail’s length is determined by the application’s requirements, and it can be cut to size for specific installations. The rail’s design often incorporates features like mounting holes and grooves to facilitate secure installation and integration into the overall machine or system. It acts as a robust base, providing a stable and precise path for linear motion.
The Carriage
The carriage, also known as the slider or block, is the moving component of a linear guide rail system. It rides along the rail, supported by linear bearings, and is responsible for carrying the load and facilitating the linear motion. The carriage is typically made of high-strength materials, such as steel or aluminum, and its design is optimized for smooth movement and load capacity. The carriage can be equipped with features like mounting holes, slots, or grooves for attaching the load or other components. The carriage’s size and design are critical for determining the load capacity and the overall performance of the linear guide rail system.
Linear Bearings
Linear bearings are the heart of a linear guide rail system, enabling smooth and precise linear motion. They are rolling elements that provide low-friction contact between the carriage and the rail. Linear bearings are typically made of hardened steel balls or rollers, which are recirculated within a raceway to minimize friction and wear. The type of bearing used (ball or roller) influences the load capacity, speed, and accuracy of the system. Linear bearings are designed for high-precision applications, providing minimal play and smooth operation, even at high speeds and under heavy loads. Their ability to handle significant forces while maintaining accuracy makes them essential for various industrial machinery and automation applications.
Advantages of Linear Guide Rails
Linear guide rails offer numerous advantages, making them ideal for various industrial applications. They provide high precision, low friction, high load capacity, and long service life, ensuring reliable and efficient operation.
High Precision and Accuracy
Linear guide rails are renowned for their exceptional precision and accuracy. This is due to the use of rolling elements, such as balls or rollers, which provide smooth and low-friction movement. The recirculating ball or roller bearings within the carriage ensure consistent linear motion along the rail, minimizing deviation and ensuring precise positioning. This high precision is crucial in applications where accurate positioning and repeatability are paramount, such as machine tools, robotics, and automation systems.
The use of hardened steel rails and precise machining techniques further contributes to the high accuracy of linear guide rails. The tight tolerances and smooth surfaces minimize friction and wear, ensuring consistent performance over extended periods. This precision is vital for maintaining tight tolerances in manufacturing processes and ensuring consistent product quality.
Low Friction and Smooth Operation
Linear guide rails are designed to minimize friction and ensure smooth operation. This is achieved through the use of rolling elements, such as balls or rollers, which reduce the contact area between the moving parts. The recirculating ball or roller bearings within the carriage allow for smooth and effortless movement along the rail, reducing wear and tear on the system. This low friction characteristic is crucial for achieving high speeds and smooth linear motion, especially in applications where rapid acceleration and deceleration are required.
The smooth operation of linear guide rails also contributes to reduced noise levels and vibration. This is particularly important in environments where quiet operation is essential, such as hospitals, laboratories, and manufacturing facilities. The low friction and smooth operation also lead to increased energy efficiency, reducing the power required to move the load, which can translate into significant cost savings over time.
High Load Capacity
Linear guide rails are designed to withstand substantial loads, making them suitable for a wide range of applications. The load capacity of a linear guide rail depends on factors such as the size and type of rail, the number of carriage blocks, and the material used in its construction. The use of high-quality materials, such as hardened steel, ensures the structural integrity and durability of the system, enabling it to handle heavy loads without deformation or premature wear.
Linear guide rails are often used in applications that involve heavy machinery, such as industrial robots, automated guided vehicles (AGVs), and machine tools. They can support the weight of the moving components, ensuring stable and reliable linear movement. The high load capacity also allows for the use of linear guide rails in applications where heavy objects need to be moved precisely and efficiently, such as in material handling systems and assembly lines.
Long Service Life
Linear guide rails are known for their exceptional durability and long service life. This is attributed to their robust construction, high-quality materials, and precision manufacturing processes. The use of hardened steel raceways and rolling elements, combined with effective lubrication, minimizes wear and tear, ensuring smooth operation over extended periods. Linear guide rails are designed to resist corrosion and environmental factors, further contributing to their longevity.
The long service life of linear guide rails translates into reduced maintenance costs and downtime; They can operate reliably for years without requiring frequent replacements or repairs. This makes them a cost-effective solution for applications where continuous operation and minimal downtime are essential, such as in manufacturing, packaging, and material handling industries.
Choosing the Right Linear Guide Rail
Selecting the right linear guide rail is crucial for optimal performance and longevity in your application. Several factors need consideration, including load capacity, speed requirements, accuracy needs, and environmental conditions. A well-informed choice ensures smooth operation, precision, and long-term reliability.
Factors to Consider
When selecting a linear guide rail, several factors must be carefully considered to ensure the best fit for your specific application. These include⁚
- Load Capacity⁚ The maximum weight the linear guide rail can support without compromising performance or causing damage. This is crucial for determining the stability and reliability of the system.
- Speed Requirements⁚ The desired speed of movement for the guided component. Faster speeds often require different bearing designs and materials to handle the increased forces.
- Accuracy Needs⁚ The level of precision required for the linear motion. Some applications demand high accuracy, while others tolerate a greater degree of variance.
- Environmental Conditions⁚ Factors such as temperature, humidity, and exposure to contaminants can influence the choice of materials and coatings for the linear guide rail.
- Installation Space⁚ The available space for mounting and operating the linear guide rail system. This includes considerations for the overall size, mounting points, and clearances.
- Budget⁚ Linear guide rails vary in price depending on their features, materials, and complexity. Setting a realistic budget helps narrow down potential options.
By carefully considering these factors, you can select the most suitable linear guide rail to meet your specific needs and ensure optimal performance in your application.
Types of Linear Guide Rails Available
Linear guide rails come in a variety of types, each with unique characteristics and applications. Understanding these differences is crucial for choosing the right type for your specific needs. Some common types include⁚
- Ball Bearing Linear Guide Rails⁚ These are the most common type, featuring recirculating balls within the bearing block that roll along the rail. They offer low friction, high speed capabilities, and are suitable for a wide range of applications.
- Roller Bearing Linear Guide Rails⁚ Featuring cylindrical rollers instead of balls, these offer higher load capacities and greater rigidity. They are well-suited for applications requiring heavy loads and demanding operating conditions.
- Miniature Linear Guide Rails⁚ Designed for compact applications, these offer high precision and smooth movement in a smaller footprint. They are commonly used in robotics, medical devices, and other applications where space is limited.
- Linear Slide Rails⁚ These are similar to linear guide rails but feature a simpler design and lower load capacities. They are often used in applications where precision is not a critical factor.
- Linear Bushings⁚ These are self-lubricating bearings that can be used as linear guide rails. They are commonly found in applications where low friction and quiet operation are essential.
The choice of linear guide rail type ultimately depends on the specific requirements of your application, such as load capacity, speed, accuracy, and environmental conditions. Consulting with a technical expert can help ensure you select the most appropriate type for your needs.
Popular Linear Guide Rail Manufacturers
Several companies are prominent in the linear guide rail industry, each offering a wide range of products and services to meet various needs. Some of the most recognized and respected manufacturers include⁚
- THK⁚ A Japanese company known for its high-quality linear motion products, including linear guide rails, ball screws, and linear actuators. They offer a wide selection of sizes and configurations, making them a popular choice for various applications.
- HIWIN⁚ Another leading manufacturer from Taiwan, HIWIN provides a comprehensive range of linear guide rails, ball screws, and other linear motion components. They are known for their innovative designs and competitive pricing.
- NSK⁚ A Japanese company with a long history in bearings and linear motion technology. NSK offers a wide variety of linear guide rails, linear bearings, and other components known for their precision, durability, and reliability.
- HepcoMotion⁚ A UK-based company specializing in linear motion systems, including linear guide rails, ball screws, and linear actuators. They are known for their high-quality products and innovative solutions.
- Bosch Rexroth⁚ A German multinational company offering a wide range of industrial automation solutions, including linear guide rails, linear actuators, and other components. They are known for their robust products and advanced technologies.
These manufacturers are just a few of the many companies that produce high-quality linear guide rails. When choosing a supplier, consider factors such as product quality, technical support, lead times, and pricing.
Installation and Maintenance
Proper installation and regular maintenance are crucial for ensuring optimal performance and extending the lifespan of linear guide rails.
Installation Process
Installing linear guide rails requires careful attention to detail to ensure proper alignment and smooth operation. The process typically involves the following steps⁚
- Preparation⁚ Clean the mounting surfaces thoroughly to remove any debris or contaminants that could interfere with the installation.
- Mounting⁚ Secure the rails to the mounting surface using appropriate fasteners. Ensure that the rails are properly aligned and parallel to each other.
- Carriage Installation⁚ Install the carriage onto the rails, making sure it slides smoothly and without any binding.
- Lubrication⁚ Apply a suitable lubricant to the bearings and rails to reduce friction and wear. Refer to the manufacturer’s recommendations for the appropriate type and amount of lubricant.
- Testing⁚ Once the installation is complete, test the linear guide rail system to ensure proper functionality and smooth operation.
It is important to follow the manufacturer’s instructions carefully and use the recommended tools and equipment during the installation process. Proper installation ensures accurate movement, reduces wear and tear, and extends the life of the linear guide rails.
Maintenance Tips
Regular maintenance is essential for ensuring the long-term performance and lifespan of linear guide rails. Here are some essential maintenance tips⁚
- Lubrication⁚ Apply a suitable lubricant to the bearings and rails regularly, following the manufacturer’s recommendations. Proper lubrication minimizes friction and wear, ensuring smooth operation and extending the life of the system.
- Cleaning⁚ Clean the rails and bearings periodically to remove dirt, debris, and contaminants that can accumulate over time and hinder smooth operation. Avoid using harsh chemicals that can damage the rail surface.
- Inspection⁚ Inspect the rails and bearings for signs of wear, damage, or misalignment. Replace worn or damaged components promptly to prevent further damage and ensure continued accuracy.
- Environmental Protection⁚ Protect the linear guide rails from harsh environments such as excessive dust, moisture, or extreme temperatures. These factors can accelerate wear and shorten the system’s lifespan.
- Proper Handling⁚ Avoid overloading the linear guide rails beyond their rated capacity. Handle the system with care to prevent damage and ensure long-term performance.
By following these maintenance tips, you can significantly extend the lifespan of your linear guide rail system, ensure reliable performance, and minimize downtime in your operations.